Usted hace un seguimiento cuidadoso de las ventas, los números de producción diaria y completa una declaración de pérdidas y ganancias al final de cada mes. Esto puede ser suficiente para cumplir con los requisitos del gobierno y satisfacer a los accionistas; además de proveer suficiente información para mantener el flujo de trabajo, pero los informes estándar sobre los que se basan la mayoría de las empresas de plásticos sólo muestran la punta del iceberg. Hay muchísima información valiosa adicional escondida en el proceso (bajo la superficie), en la medición de la producción, el consumo de material, y las horas que pueden ayudarle a mejorar el rendimiento, reducir los costos y mejorar la tasa de procesamiento de su planta de fabricación de plásticos. Si sólo está viendo la punta del iceberg de la información, es posible que se esté perdiendo de mucho. Hacer caso omiso de esta información oculta representa una amenaza para el buen estado de su negocio.
De manera global, la gestión de la producción y el inventario es en realidad la suma de la gestión de los recursos individuales al interior del negocio – máquinas individuales, personal, materiales y productos. Y así como la cadena es apenas tan fuerte como su eslabón más débil; los recursos que presentan un bajo rendimiento o que se encuentran en condiciones de desafío pueden afectar de manera negativa el rendimiento de toda la compañía.
Por lo tanto, es importante medir, monitorear y gestionar cada recurso de una manera tan cuidadosa y cercana como sea posible con el fin de detectar cualquier variación con respecto a las expectativas y ser capaz de aplicar las medidas correctivas antes de que se vean afectados la productividad y el rendimiento. En la fábrica digital de hoy en día, es más fácil que nunca lograr ese objetivo. Los mejores sistemas ERP / MES modernos están construidos de manera que permitan hacer el seguimiento continuo de las medidas clave de la velocidad de la máquina, tasa de producción, eficiencia, calidad (tasas de rechazo), utilización y otros factores para alertar a los operadores y directivos cuando las condiciones o los logros difieran de las expectativas.
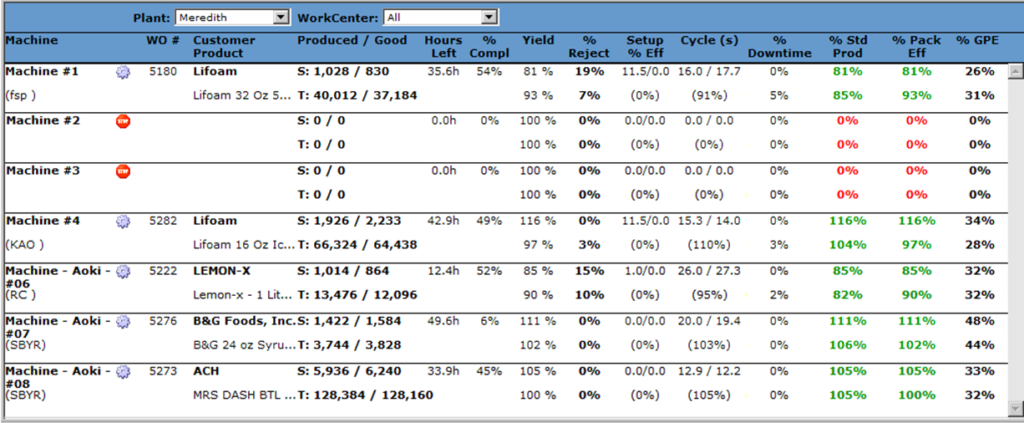
Podría decirse que la medición interna más importante a tener en cuenta es la eficiencia de la máquina: el rastreo del tiempo de ciclo – el intervalo entre las piezas sucesivas producidas – o de manera similar, la cantidad producida por hora ya sea en unidades o en libras. Dado que el tiempo de producción real es un factor importante en el costo del producto, una variación en la tasa de proyección óptima o asumida puede representar una gran diferencia en el costo del producto y las ganancias.
Sin embargo, funcionar de manera más rápida de lo “normal” no siempre es bueno, si el resultado es un menor rendimiento o una tasa superior de desechos. Por lo tanto, realizar el seguimiento de los rechazos es también muy importante y debe realizarse ya sea en tiempo real o lo más parecido posible a ello. Cuanto más temprano se detecte un problema de calidad, más temprano se podrán hacer las correcciones y menos partes defectuosas serán fabricadas.
A pesar de que el precio de la materia prima es por lo general un componente relativamente pequeño del costo de producto, la disponibilidad es crítica – que se acabe el material antes de que la cantidad requerida sea producida puede ser desastroso. La adquisición y el mantenimiento de la materia prima están ligados a las proyecciones o las reservas y a la tasa de uso. Si la tasa de uso es incorrecta, se corre el riesgo de escasez de material. Además, las suposiciones de uso inexactas en la receta o en la lista de materiales pueden dar lugar a precios incorrectos y a suposiciones erróneas acerca de los márgenes.
El seguimiento del uso real de material sirve para validar las suposiciones de la lista de materiales y proporciona información sobre el uso real, incluyendo las pérdidas de puesta en marcha y el desperdicio “normal” – toda la información que puede ser usada para mejorar el cálculo de los costos y la gestión de los materiales. El seguimiento del uso en tiempo real puede también proporcionar una alerta temprana acerca de los problemas en los procesos que pueden conducir a rechazos o problemas operacionales.
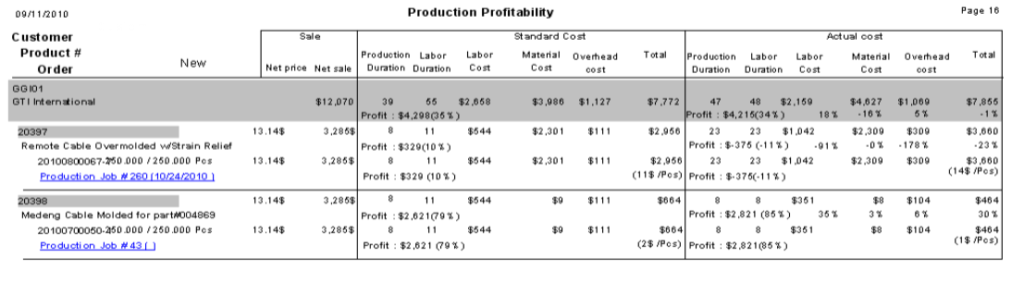
Puede sonar complicado hacer el seguimiento permanente de diversos factores en múltiples recursos, pero en realidad la medición continua y la presentación de informes son mucho más simples de lo que suena. La tecnología recopila la información detallada y realiza la evaluación inicial mediante la comparación de las mediciones reales con las esperadas y la experiencia del pasado. Solamente las desviaciones o los resultados inesperados son reportados de manera inmediata a las personas responsables para el seguimiento o la investigación más a fondo. La información recopilada siempre estará disponible, por supuesto, para fines de estudio y mejora del rendimiento. Esto contrasta con la necesidad de responder a un problema de calidad, tiempo de producción o sobrecosto después de los hechos – sin ninguna pista acerca del origen y la ubicación del problema.
El Titanic tuvo su desafortunado encuentro con la parte inferior del iceberg que se encontraba sumergida, en un momento en el que el radar, el sonar y las herramientas de navegación y las comunicaciones modernas aún no existían. Hoy en día, un hundimiento causado por un encuentro con un iceberg es inimaginable simplemente debido a la tecnología disponible y en uso en todos los buques de alta mar. Los fabricantes de plásticos tienen acceso al equivalente de sonar y radar para el control de las actividades y los recursos en la planta que pueden revelar la existencia e incluso la posibilidad emergente de peligros ocultos tales como una variación inesperada en la tasa de producción, el cambio en los desechos o el rendimiento, o el uso inusual de material. Los directivos pueden usar estas señales para ajustar de manera proactiva el rendimiento al reducir los desechos, disminuir los costos, mejorar la finalización a tiempo, y preservar el margen.